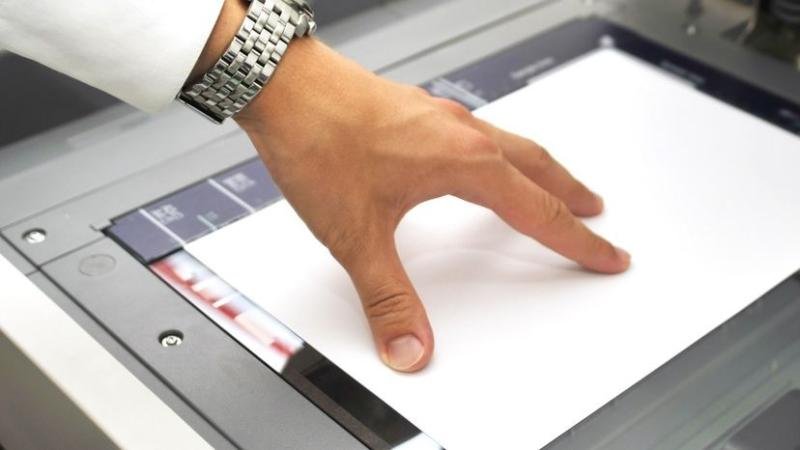
Setting up a scanner production facility requires detailed market analysis in addition to detailed insights into various operational aspects, including unit processes, purchasing raw materials, utilities, infrastructure arrangement, machines and technology specifications, personnel planning, logistics and financial reasons.
The report of Imarc Group entitled “Scanner Manufacturing Plant Project Report 2025: Industry Trends, Plant Setup, Machinery, Raw Materials, Investment Possibilities, Costs and Income” offers an extensive guide for setting up a scanner production factory, with everything from product overview and production processes to detailed financial insights.
Get Scanner -Fabriekkostenraging Report: https://www.imarcgroup.com/scanner-babricage-plant-project-report/requestsample
A scanner is an electronic device that is used to convert physical documents, images or objects into digital formats for storage, editing or transmission. Often working in industries such as health care, production, retail and education, scanners range from flatbed and handheld models to advanced 3D and barcode scanners. These devices facilitate efficient data digitalization and integration in digital workflows, to support an improved operational accuracy and speed. Technological progress, including improved optical character recognition (OCR) and integration with cloud-based platforms, have expanded scannet applications in both business and consumer environments.
The global scanners market witnesses steady growth, driven by an increasing demand for digital transformation in various industries. Important market factors include the widespread acceptance of automation in business processes, the growing need for document management systems and the increasing implementation of identification and tracking technologies in logistics and health care. In addition, the e-commerce boom and the expansion of the use of barcode and QR codescanis are the question, especially in the inventory and supply chain management. Innovations in 3D scanning and portable scanning solutions also contribute to market expansion, catering for sectors such as architecture, automotive and medical diagnostics.
Most important steps needed to set up a scanning factory
1. Market analysis
The report provides insight into the landscape of the scanner industry at the global level. The report also offers a segmental and regional disintegration of the global scanner industry. Moreover, it also offers the price analysis of raw materials used in the production of scanner, together with the profit margins in the industry.
• Segment breakdown
• Regional insights
• Price analysis and trends
• Market forecast
2. Product production: Detailed process current
Detailed information with regard to the process flow and various unity operations involved in the Scanner Manufacturing Plant Project is worked out in the report. These include:
• Country, location and site-Development
• Plant classification
• Plant machines
• Purchasing of raw material
• Packaging and storage
• Transport
• Quality inspection
• utilities
• Requirements and wages of Human Resources
• Marketing and distribution
3. Project requirements and costs
The report offers a detailed location analysis about insights in the factory location, selection criteria, location sign, environmental impact and expenditure for the preparation of the scanner factory. Moreover, the report also provides information with regard to the layout of the plant and factors that influence the same. In addition, other requirements and expenditure with regard to machines, raw materials, packaging, transport, utilities and human resources have also been dealt with in the report.
Machines and equipment
• List of machines required for scanner production
• Estimated costs and suppliers
Raw material
• Types of materials required and sourcing strategies
Utilities and overhead costs
• Electricity, water, labor and other operational costs
4. Project economy
A detailed analysis of the project economy for setting up a scanning factory is illustrated in the report. This includes the analysis and detailed understanding of capital expenditure (Capex), operational expenses (OPEX), income projections, taxes, depreciation, liquidity analysis, profitability analysis, payback time, NPV, uncertainty analysis and sensitivity analysis.
Capital expenses (Capex)
• First installation costs: land, machines and infrastructure
Company expenditure (OPEX)
• Recurring costs: raw materials, labor, maintenance
Income projections
• Expect income based on production capacity, target market and market demand
Tax
Depreciation
Financial analysis
• Liquidity analysis
• profitability analysis
• Personal period
• Net current value (NPV)
• internal return
• Profit and loss account
Uncertainty analysis
Sensitivity
Economic analysis
Ask an analyst: https://www.imarcgroup.com/request?type=report&id=12062&flag=c
5. Legal and regulatory compliance
• Licenses and permits
• Regular procedures and approval
• Certification requirement
6. Rent and training
• Total requirement of Human Resource
• Salary cost analysis
• Overview of the employee policy
The report also includes critical insights into important success and risk factors, which emphasize the aspects that influence the success and potential challenges in the industry. In addition, the report includes strategic recommendations, offering useful advice to improve the operational efficiency, profitability and competitiveness of the market. An extensive case study of a successful company is also provided that present best practices and examples of an established company, which can serve as a valuable reference for newcomers on the market.
About us:
IMARC is a global market research company that offers extensive services to support companies in every phase of growth, including market access, competition inflatations, purchasing research, approvals for regulations, factory setup, business admission and recruitment. Specialized in factory institutions solutions, we offer detailed financial cost modeling to assess the feasibility and financial viability of setting up new production factories worldwide. Our models relate to capital expenditures (Capex) for land acquisition, infrastructure and installation of equipment, while also evaluates the influence of the factory out and the impact of the factory on operational efficiency, energy consumption and productivity. Our holistic approach offers valuable insights into trends in the industry, strategies for competitors and emerging technologies, so that companies can optimize the activities, control control costs and stimulate long -term growth.
Contact us:
Imarc group
134 N 4th St. Brooklyn, NY 11249, USA
E -Mail: [email protected]
Tel No: (D) +91 120 433 0800
United States: +1-631-791-1145
This release is published on OpenPR.